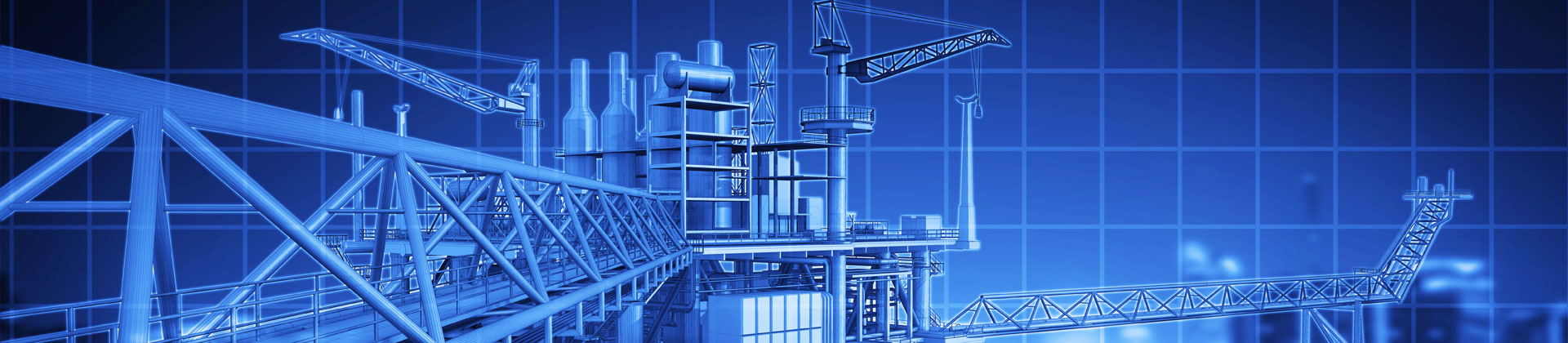
Erasmian uses 3D Scanning to create 3D models & 2D drawings from existing plant & equipment to support maintenance, refurbishment, up-scaling or asset management. Up-to-date models and drawings may increase plant value and allow for financial valuation. We have assisted clients of all sizes in Africa, Middle East and Europe.
A high-end 3D laser scanning device is used to scan structures or process plant for different purposes. These deliverables can be used in the following applications:
BETTER MAINTAINABILITY
IMPROVED ASSET MANAGEMENT
ALLOWS VALUATION
COMPLETES DESIGN LIBRARY
Here is a short video (quality reduced to save your download time) illustrating just one aspect of a laser scanning result:
The contracting process follows a simple workflow where a cost offer is prepared based on a detailed conversation with our client to determine the deliverables for the scan product. This can be from delivering a simple raw scan data set, to a registered data set where the point cloud can be imported into a CAD package like AutoCAD or Inventor through to the creation of a 3D solid model based on the scan data.
Additionally, GIS information can be attached to the scan information to place the 3D information within the context of a coordinate system. This depends on the level of accuracy required in the deliverables. Typical accuracies obtained are in the sub 50mm range, as per client requirements.
We only showcase SOME of the scan to 3D projects we did, due to confidentiality and space considerations (contact us re consulting work done in your industry):
Conversion of 3D scan to solid 3D model using AutoCAD software. This was an as-built deliverable which the client used to plan future project developments. The client was a South African based technology supplier to a Gauteng based metal recycling plant.
Using a 3D scan of an underground chamber in a Zambian based copper mine, to design and model an underground ore crushing plant. The crusher plant had to align with an existing ore-pass for the vibrating grizzly to receive the incoming rock, before screening and crushing. The discharge happened via a conveyor into the next ore pass to a lower tunnel where the main conveyor transported the crushed ore further.
Using a scan of an existing iron ore processing plant for the layout and design of a new ore screening, crushing, and conveying plant. This involved tying into the existing plant at several points which required a high level of accuracy to prevent major site work during construction. The result was achieved due to the 3D scan being used with the relevant accuracy and site information.